Analiza Techniczna i Badania Przydomowej Biogazowni Rolniczej
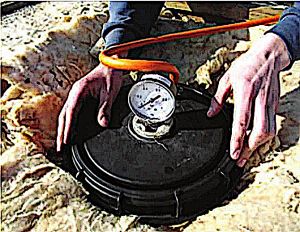
Analiza Techniczna Przydomowej Biogazowni Rolniczej
Źródło: Artykuł "Przydomowa biogazownia rolnicza", Elektronika Praktyczna 12/2014 oraz materiał wideo prezentujący instalację.
Autorzy oryginalnego artykułu: Michał Nawrot, Marcin Janiczek
1. Wprowadzenie
W artykule oraz materiale wideo przedstawiono projekt, budowę oraz wyniki badań przydomowej, zautomatyzowanej biogazowni rolniczej o niewielkich wymiarach. Głównym celem projektu było rozwiązanie problemu nieprzyjemnego zapachu gnojowicy oraz produkcja biogazu na potrzeby gospodarstwa domowego. Biogaz, uzyskiwany z surowców rolniczych i odchodów zwierzęcych w procesie fermentacji metanowej, może być wykorzystany do produkcji prądu, ciepła lub jako gaz do gotowania. Przefermentowany substrat stanowi wartościowy, bezwonny nawóz.
Technologia ta jest szeroko stosowana w krajach takich jak Szwecja, Dania, Niemcy czy Austria. W Polsce, mimo korzystnych zapisów w Prawie Energetycznym (znowelizowanym w 2009 r.), jej zastosowanie jest wciąż ograniczone, lecz dynamicznie rozwijające się, szczególnie w kontekście małych instalacji (do 100 kW) niewymagających koncesji.
2. Motywacja i Cele Projektu
Autorzy podjęli się budowy instalacji z powodu uciążliwości zapachowych związanych z wywożeniem gnojowicy na pola. Kluczowymi celami projektu było:
- Zbudowanie zautomatyzowanej instalacji minibiogazowni dla niewielkiego gospodarstwa rolnego, w dużej mierze z materiałów z odzysku.
- Przeprowadzenie badań dotyczących ilości wytwarzanego gazu w zależności od temperatury panującej w komorze fermentacyjnej.
- Uzyskanie biometanu do spalania w silnikach (prąd/ciepło) lub do zasilania kuchenki gazowej.
- Neutralizacja nieprzyjemnego zapachu gnojowicy przy zachowaniu jej właściwości nawozowych.
3. Opis Techniczny Instalacji
Zaprojektowana i zbudowana instalacja składała się z następujących głównych podzespołów:
3.1. Komora Fermentacyjna
- Zbiornik: Używany zbiornik o pojemności 1000 litrów, typu Mauser (często spotykany jako zbiornik IBC), wykonany z polietylenu wysokiej gęstości (HDPE). Materiał ten charakteryzuje się dobrą odpornością na warunki zewnętrzne, większość kwasów, zasad i chemikaliów. [2, 6] Zakres temperatur pracy dla HDPE to typowo od -40°C do +70°C lub nawet -50°C do +80°C, co zapewnia stabilność strukturalną w warunkach pracy biogazowni. [2, 4, 7] Zbiornik był wypełniany w 90% objętości substratem fermentacyjnym (gnojowicą z niewielką ilością kiszonki). Górna część zbiornika charakteryzowała się elastycznością, działając jako swego rodzaju membrana, która wybrzuszała się pod wpływem produkowanego gazu. Pozostawiono odpowiednią przestrzeń, aby zapobiec uszkodzeniu izolacji przez to wybrzuszenie. (Fotografia 1 przedstawia ogólny widok instalacji).
- Izolacja i Ogrzewanie: Zbiornik obudowano drewnianym stelażem, umożliwiającym montaż izolacji z waty mineralnej i styropianu (Fotografie 3, 5, 7, 8). Ogrzewanie realizowane było za pomocą wężownicy z rury do ogrzewania podłogowego (8 zwojów) owiniętej wokół zbiornika (Fotografia 4). Przepływ ciepłej wody (np. z instalacji solarnej, pieca C.O. lub, na potrzeby testów, z bojlera elektrycznego o mocy 2000W) był sterowany przez elektrozawór. System ogrzewania wykazywał dobrą sprawność – dostarczenie wody o temperaturze ok. 40°C do wężownicy pozwalało w ciągu ok. 3 godzin uzyskać temperaturę wsadu ok. 30°C, a dobra izolacja umożliwiała długie utrzymanie temperatury.
- Wzmocnienie: Konstrukcja została wzmocniona dwoma linkami stalowymi skręconymi śrubami, aby zabezpieczyć zbiornik przed rozsadzeniem przez gromadzący się gaz (Fotografia 6).
- Monitoring: Wewnątrz zbiornika znajdował się czujnik ciśnienia i temperatury. Na deklu komory zamontowano manometr do wizualizacji ciśnienia (typowo ok. 100 mbar podczas pracy).
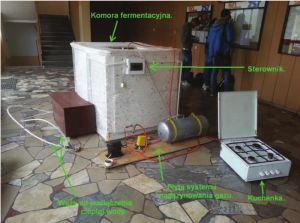
3.2. System Mieszania Substratu
Zamiast klasycznego mieszadła mechanicznego, zastosowano innowacyjny system polegający na okresowym przepompowywaniu oczyszczonej substancji płynnej z dolnej do górnej części zbiornika.
- Filtracja: Na dnie zbiornika umieszczono rurę PCV 110 mm z otworami (filtracja zgrubna), wewnątrz której znajdował się wąż drenarski owinięty otuliną (filtracja dokładna), co miało na celu ochronę pompy przed zanieczyszczeniami (Fotografie 9, 10).
- Pompa: Do przetłaczania substratu użyto pompy od automatu pralniczego o mocy 30W.
- Dystrybucja: Oczyszczony płyn był kierowany przez pompę i czwórnik rozprowadzający (Fotografia 13, 14) do czterech węży zakończonych dyszami, wprowadzonymi do wnętrza komory (Fotografia 15).
- Czas Pracy: Pompka pracowała cyklicznie, zazwyczaj w godzinach nocnych, przez około 5 godzin.
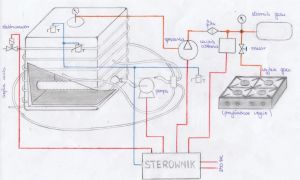
3.3. System Magazynowania Gazu
- Pomiar Produkcji: Ilość wytworzonego gazu mierzona była manometrem.
- Oczyszczanie i Kompresja: Biometan trafiał do sprężarki (z agregatu lodówkowego, zdolnej do uzyskania ciśnienia 20 bar), a następnie przez filtr/osuszacz do zbiornika ciśnieniowego (Fotografia 16).
- Bezpieczeństwo: Zastosowano zawór ręczny oraz czujnik ciśnienia z alarmem.
3.4. Układ Sterowania (Sterownik Minibiogazowni)
Pracą instalacji zarządzał samodzielnie wykonany sterownik z mikrokontrolerem (Fotografia 17).
- Funkcje: Utrzymywanie temperatury, sterowanie mieszaniem i sprężarką, monitoring ciśnienia z alarmem, wyświetlanie parametrów.
- Czujniki: Temperatury (wsadu, węża grzewczego, otoczenia), ciśnienia.
- Sygnalizacja: Diody LED.
- Dodatkowe Funkcje: Możliwość przełączenia w tryb opróżniania.
- Montaż: W skrzynce ochronnej (Fotografia 18).
4. Uruchomienie i Badania Eksploatacyjne
- Napełnianie: Komora została zalana substratem (900 litrów gnojowicy z niewielką ilością kiszonki) 28.02.2014 r.
- Parametry Pracy (przykładowe): Temperatura wsadu 34°C (histereza 2°C), mieszanie nocne (ok. 5,5 h), sprężanie gazu rano (4 min).
- Obserwacje (5 tygodni):
- Produkcja CO2 od drugiego dnia.
- Palność gazu od 13. dnia.
- Pierwsze magazynowanie 15 marca.
- Wydajność: Dzienna produkcja wystarczająca na ok. 40 minut pracy kuchenki gazowej (Fotografia 19).
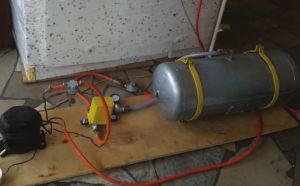
5. Badania Wpływu Temperatury na Produkcję Biogazu
Badania polegały na ustawianiu temperatury w komorze na 24h i odczycie ciśnienia (zakres 20-40°C, skok co 4°C). (Fotografie 20, 21).
Wynik: Optymalna temperatura fermentacji to 36°C ±2°C.
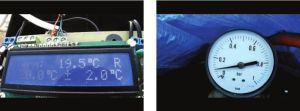
6. Wnioski i Dalsze Prace
Zbudowana biogazownia spełniła cele, produkując biogaz i neutralizując zapach gnojowicy. Kluczowe wnioski:
- Zautomatyzowany system działa stabilnie.
- Innowacyjne mieszanie jest skuteczne i energooszczędne.
- System ogrzewania jest wydajny.
- Optymalna temperatura fermentacji to 36°C ±2°C.
- Uzyskany biogaz jest użytecznym źródłem energii.
Planowano wdrożenie ciągłego procesu wymiany substratu. Projekt demonstruje potencjał małoskalowych biogazowni dla rolnictwa.
Uwaga: Numery fotografii odnoszą się do oryginalnego artykułu w "Elektronika Praktyczna" 12/2014.